
Key Features of Compression Packing
Compression packing, gland packing, or simply packing is an essential tool for controlling leakage in valves and pumps for a number of reasons. Compression packing can be made from several different types of material, natural fibers, synthetic fibers, metals, and flexible graphite. It can also be made into multiple orientations, such as braided material, bulk and twisted material, molded and machined packing, and flexible graphite tape. Compression packing’s versatile composition and orientation have made it an ideal sealing solution for a number of pump and valve applications which are used in several process and service industries, including Petrochemical, paper and steel mills, water and sewage and nuclear plants, and others. Although there are many different types of packing options, they all share the following key features:
- Lubrication
- Compressibility
- Heat and Chemical Resistance
- Non-Corrosive

Lubrication
Lubrication is a crucial component to successful operation of valves and pumps. The oil can seen above is a standard item in every workshop where repairs are made on items with moving parts. Proper lubrication is essential to reducing friction between moving parts, which results in reduced damage and better efficiency.
The same is true for valves and pumps, which both contain various moving parts. Compression packing, which is used to seal the stuffing boxes of pumps and valves against either a rotating shaft or stem, requires lubrication both during initial installation and normal operation. Lubrication for compression packing comes in various forms (solids, liquids, and semi-liquids). Compression packing gets damaged over time and must be replaced, but its usability can be maximized with the proper lubrication.

Compressibility
An effective compression packing must return to its original form after being compacted. This characteristic is known as compressibility. This can be confusing with regards to the definition in physics, where compressibility is the measure of volume change relative to a change in pressure. Compression packing doesn’t necessarily lose its volume during compaction.
In the context of compression packing, compressibility describes a packing material’s ability to “rebound” back to its original shape. In the above picture, the green apple in the vice is not compressible. If you replaced the green apple with a racquetball and compressed it with the vice it would return to its original shape, therefore the racquetball is compressible. Compression packing is subjected to pressure when the gland screws are tightened, compressing the gland against the packing material. Compression packing needs to be compressible in order to “press back” against the gland, effecting a seal.
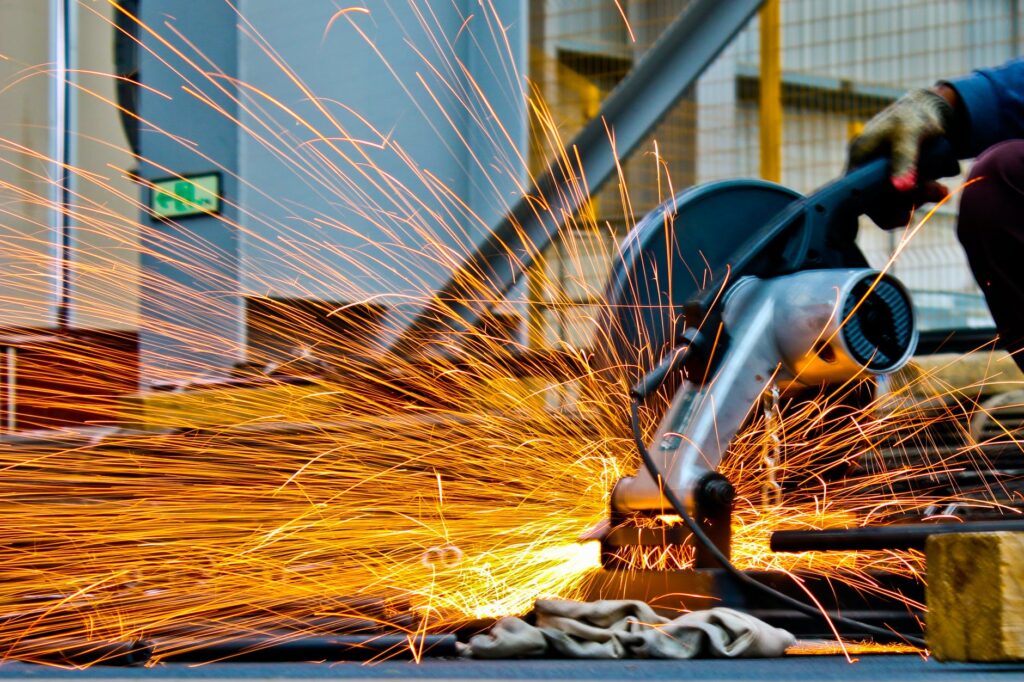
Heat and Chemical Resistance
Effective compression packing must also be resistant to high temperatures and harsh chemicals. In the picture above, sparks are seen when a circular saw cuts through metal. Sparks are generated from the friction between the metal saw blade and the metal being cut. If you have experience with using a saw you will know that the blade will get hot even if you are cutting wood. Saw blades must be heat resistant in order to cut through wood or metal successfully.
Many types of packing are subjected to intense heat caused by high temperature environments or friction from moving parts. And in many cases compression packing must also withstand harsh chemicals. As mentioned earlier, packing material comes in many different forms and materials. Compression packing material, such as flexible graphite, is both heat and chemical resistant.
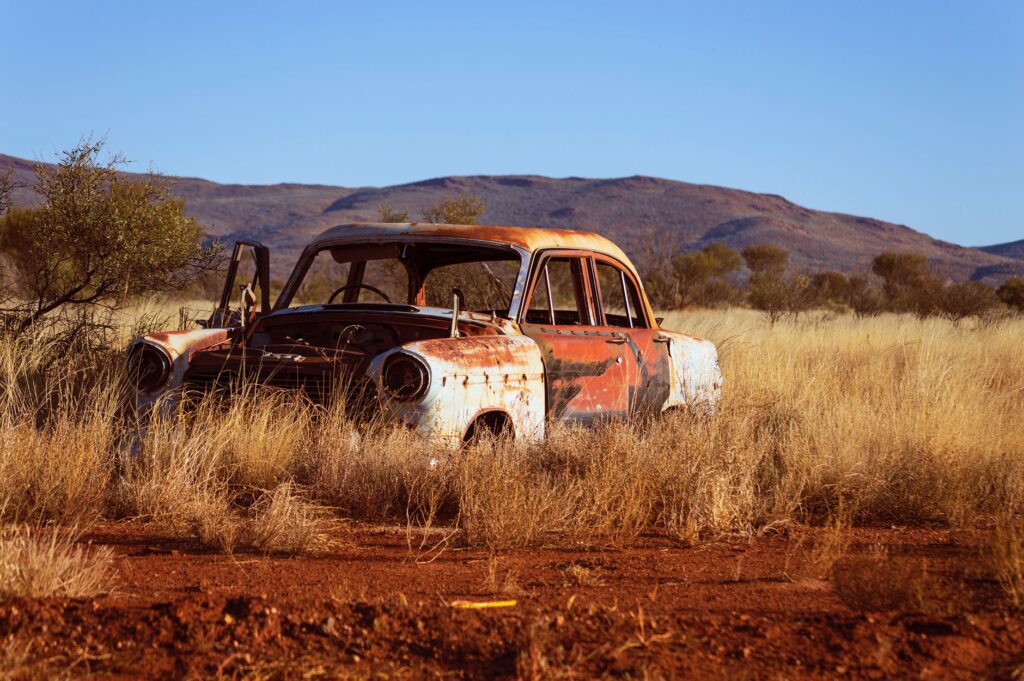
Non-Corrosive
Along with the above mentioned features, compression packing must be non-corrosive. Corrosion is a concern, not only for the pump and valve equipment, but also the medium being transferred. Corrosion occurs when there is damage due to a chemical reaction between two things. The rusted, abandoned car seen above has corroded from being exposed to the elements, namely intense sunlight and rain water.
Compression packing must be non-corrosive. An effective packing cannot react or change when it comes in contact with the equipment it is sealing or the medium it is helping transport. Pumps and valves used in the food service industry is an example of when this is important.
In a Nutshell
Lubrication, compressibility, heat and chemical resistance, and non-corrosive are all important features in packing material. But even with these characteristics, all packing material must be replaced over time. Timely replacement and proper installation are two important things to remember, even with premium packing material.